Choosing the Best Water Solution for Your Machine Shop: Is it Reverse Osmosis? Deionized Water?
By: Chris Fisk, Vice President, Acculube
“If my water is good enough to drink, it's good enough to clean with, right?”
If you’re cleaning your kitchen, yes. But if you’re using drinking water to clean your CNC machine or to mix with a machine's coolant, you may be slowly killing your machine.
That’s because the water you add has a powerful effect on the quality of the product. Water-mixable products such as coolants and cleaners are 90 percent water and 10 percent active ingredients. Bad water will turn even the best coolant or cleaner into a rust-inducing liquid.
Water Varies
A manufacturing plant may access water from a well, reservoir, lake, or river. Other factors affecting water quality include the local geology, the amount and type of sediment, and temperature. Even the change of seasons has an effect. A test of your water in January will yield different results in July.
What To Test For
The first step toward quality water is to test your water supply for the following additives. Suppliers, including Acculube, can test your water, or you can send samples to an independent lab.
Chloride
Chloride is a naturally-occurring chemical in water. It can also be added during municipal water treatment. However, high levels can cause rust. The acceptable amount of chloride is dependent on the type of coolant or cleaner you use. A common rule is to use water with a chloride level below 20 parts per million.
Sulfate, Sulfur and Other Dissolved Gases
Similar to chloride, high levels (above 40 parts per million) of dissolved gases in the water can cause rust.
Hardness and Softness
Water can be “too clean.” If water is too pure, it affects pH levels, takes on acid properties and becomes corrosive. Some coolants contain oil and include an emulsifier to hold the water and oil in solution. If water is too soft, it causes the emulsifier to foam like a detergent. If water is too hard, the abrasiveness will ruin the emulsifier molecule and the coolant will separate. The goal is to find the happy median. Water hardness should be between 100 to 200 parts per million.
Sodium, Magnesium, Calcium and other Minerals
Using any water-mixable product in a manufacturing application involves evaporation. The problem is that while the water evaporates, the minerals in the water don't. Minerals act like sand paper on a microscopic level. They break down the coolant or cleaner, reducing the product's service life. Minerals are part of the water's hardness. Again, water hardness should be between 100 to 200 parts per million.
How To Clean Your Water
The most economical solution to improving water quality is to find a product tailored to your type of water. There are specially-formulated cleaners and coolants for soft or hard water. However, in some parts of country - including parts of Ohio and Indiana - water hardness is outside their range. When this happens, water treatment is needed. The two most popular are Dl (deionized water) and reverse osmosis.
Deionized water (DI)
Dl adds a chemical charge to the water to drop out the hardness. This is the process used to make bottled water; it produces water that is 100% pure.
Dl is less expensive to install, as equipment is not needed: you only pay for plumbing costs. However, it is more expensive to operate long-term. The chemical reaction takes place in a cylinder, which depletes and has to be replaced, sometimes as often as weekly. The average cost of a cylinder is $200.
Reverse Osmosis
Reverse osmosis uses a membrane with microscopic holes that acts as a filter. Forcing the water through the filter removes minerals and dissolved gases and produces 90% pure water.
Reverse osmosis is more expensive upfront, costing about $10,000 to $20,000 for the filter unit and installation. Long-term maintenance costs are less than Dl, with only about $200 spent every few months to clean the membrane of collected minerals.
Which method to use depends on what you're manufacturing. For most industrial applications, the 90% pure water produced by reverse osmosis is sufficient. However, some manufacturers - such as those who produce medical devices – may need 100% pure water, which only the Dl process can produce.
ABOUT THE AUTHOR: Chris Fisk is Vice President of Acculube, a Dayton-Ohio based supplier of metalworking and manufacturing fluids to American manufacturers, machine shops and vehicle fleets.
NEXT ESSAY
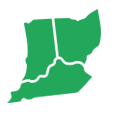 |
|
Get great advice about shop water quality and about maintaining your industrial machines and vehicles. Email Acculube or call us at 1.800.404.2570.
|
|