Lubricant Contamination Allows Varnish to Vandalize Your Machines
If you're facing decreasing production, increasing repairs and mounting machine cleaning costs, varnish may be the culprit.
By: Chris Fisk, Vice President, Acculube
Lubricant varnish is a hard organic residue that is difficult to remove. It is also a silent machine killer that slowly causes systems to deteriorate. You do everything you know regarding maintenance, yet still your machines are plagued with varnish.
The secret to all of your machine troubles could be oil; specifically, the wrong choice in oil.
Companies that use the correct oil enjoy optimum protection on high-demand applications, and long oil life. With premium lubricant, there are no fears that varnish will compromise machine performance.
The Virtue of Balance
Your machines need a lubricant that provides protection and ensures peak performance. This lubricant should be well balanced and developed with the application in mind.
Many lubricant products are not well balanced. They contain insufficient additives, or additives that counteract each other because of poor chemistry, or incorrect additive concentrations.
An unbalanced formulation usually leads to increased maintenance, unplanned downtime, shorter equipment life, and ultimately higher operating costs. In contrast, a balanced formulation achieves the standards of what oil should do for your systems.
The correct additive package protects the equipment and the oil. Equipment is safeguarded from everyday wear, contamination, and rapid oil aging. These lubricants have an exceptional resistance to varnish and sludge formation that keeps systems clean and operational.
Why Worry About Contamination?
One of the primary factors in how long, and how well, equipment performs is contamination of the oil by water, dirt and other particulates. A dirty system causes wear, corrosion and deposit formation.
No matter what additives are in the oil, if contamination cannot be controlled and the system kept clean, oil and machine life will be compromised. With contamination control, premium hydraulic oils protect your equipment. This protection includes minimizing the formation of deposits that can plug filters and gum-up valves, providing a shield against rust and corrosion, and creating a healthy overall system that operates properly with low levels of contaminates.
Worried That it is Too Late to Switch?
Using the wrong lubricant can wreak havoc on your system, and damage it beyond repair if the problem is not identified quickly. Some systems are too far-gone, but for most, there is the opportunity to turn things around.
A system cleaner can slowly eliminate the varnish built up within the machine. A premium lubricant can help with this cleanup process, and prevent it from reoccurring.
While it might seem odd that one oil can fix a problem that another oil created, correctly-made oil will clean up any varnish deposits it contacts. Additives in this lubricant pick up deposits and suspend them in the fluid so that the filter can remove them.
This process is achieved only by oil formulated with additives that help in the suspension process and in a system whose filters perform properly.
Investigate cleanliness issues, sticking valves, and your current oil brand, and let’s discuss how a change in product can pay real and immediate dividends for your production, and your machine life.
ABOUT THE AUTHOR: Chris Fisk is Vice President of Acculube, a Dayton-Ohio based supplier of metalworking and manufacturing fluids to American manufacturers, machine shops and vehicle fleets.
NEXT ESSAY
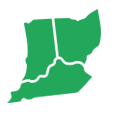 |
|
Get great advice about choosing the best lubricants, and maintaining your industrial machines and vehicles. Email Acculube or call us at 1.800.404.2570.
|
|