How to use a Grease Gun
to Lubricate Plain Bearings?
A simple grease gun is probably the most common tool for re-lubricating machine components, especially bearings. Its purpose is to direct lubricating grease to a specific point with the aid of a special fitting.
Types of Grease Guns
Grease guns of different designs are used in different applications. The most common types are lever, pistol grip and hand grip varieties. Most are mechanically driven by hand, though there are models that are air- or battery-powered (used especially to move large amounts of grease). Most common is the lever style which is also the least expensive.
A host of different bearing designs are found on machinery today. Many employ rolling elements, but simpler designs consist of just a bearing surface and another element, called a journal, that comes in contact with it. Such a bearing is called a plain bearing, the simplest type of which is a shaft rotating in a hole. As the simplest type, plain bearings are also the least expensive. They are compact, with a high load-bearing capacity. In rotary applications, machines are often fitted with bushings, which are often inserted into a housing to provide a bearing surface for a rotating shaft.
Grease vs. Oil
In some applications, plain bearings never require re-lubrication through the life of the equipment. Most plain bearings, however, require re-lubrication at some point to prevent failure. Plain bearings may be lubricated by oil, but grease has several advantages over oil, among which are:
- Lower lubricant leakage from the bearing, meaning less lubricant is required.
- When the machinery is shut down, grease's relatively high viscosity keeps it from draining out while in a static condition. Because grease remains in the bearing, there is a lubricating film available to the bearing surface as soon as the machinery is started, thus decreasing the wear due to initial start-up torque from a dead stop.
- Retained grease acts as a bearing seal to prevent grit, dust, moisture and other contaminants from entering the bearing surface, thus protecting it from premature wear.
A disadvantage of grease is that, because grease is not continually replenished in the system, the bearing runs hotter than in a system using circulating oil, which acts also as a coolant. At high speeds or under high loads, oil may be used for its cooling properties instead of grease.
But for most plain bearings that use grease, re-lubrication with every shift is a common practice. Sometimes re-lubrication is more frequent, some times less, according to the application and equipment needs. Grease guns are used for this process and here's how to do it.
- First, clean the grease fittings on the gun and the machine before connecting the two. Recognize that a volume of new grease forces the same volume of old grease out the other end of the bearing.
- Apply the right grease until new grease appears at both ends of the bearing. Leave some excess grease at exposed ends of the bearing to act as a seal and prevent contaminants from entering the system.
- In some applications, two or more different types of greases may be required to service your equipment. If so, use a separate grease gun for each type of grease to prevent cross-contamination of greases. When using different greases, select greases that are compatible in the event cross contamination occurs during maintenance.
Acculube understands that grease guns play a huge role in keeping equipment running smoothly. If you're having issues with guns or greases, or just want a better alternative to products you're using, give us a call. Our lubrication experts are quick on the draw and have unsurpassed expertise in greases and their application.
NEXT ESSAY
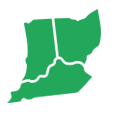 |
|
Talk with Us Today
Call the cutting oil experts at Acculube. We'll help you get the most value from every fluid you buy, and avoid the common pitfalls that can cost you money.
Contact Us: 1.800.404.2570 or email us at sales@acculube.com
|
|